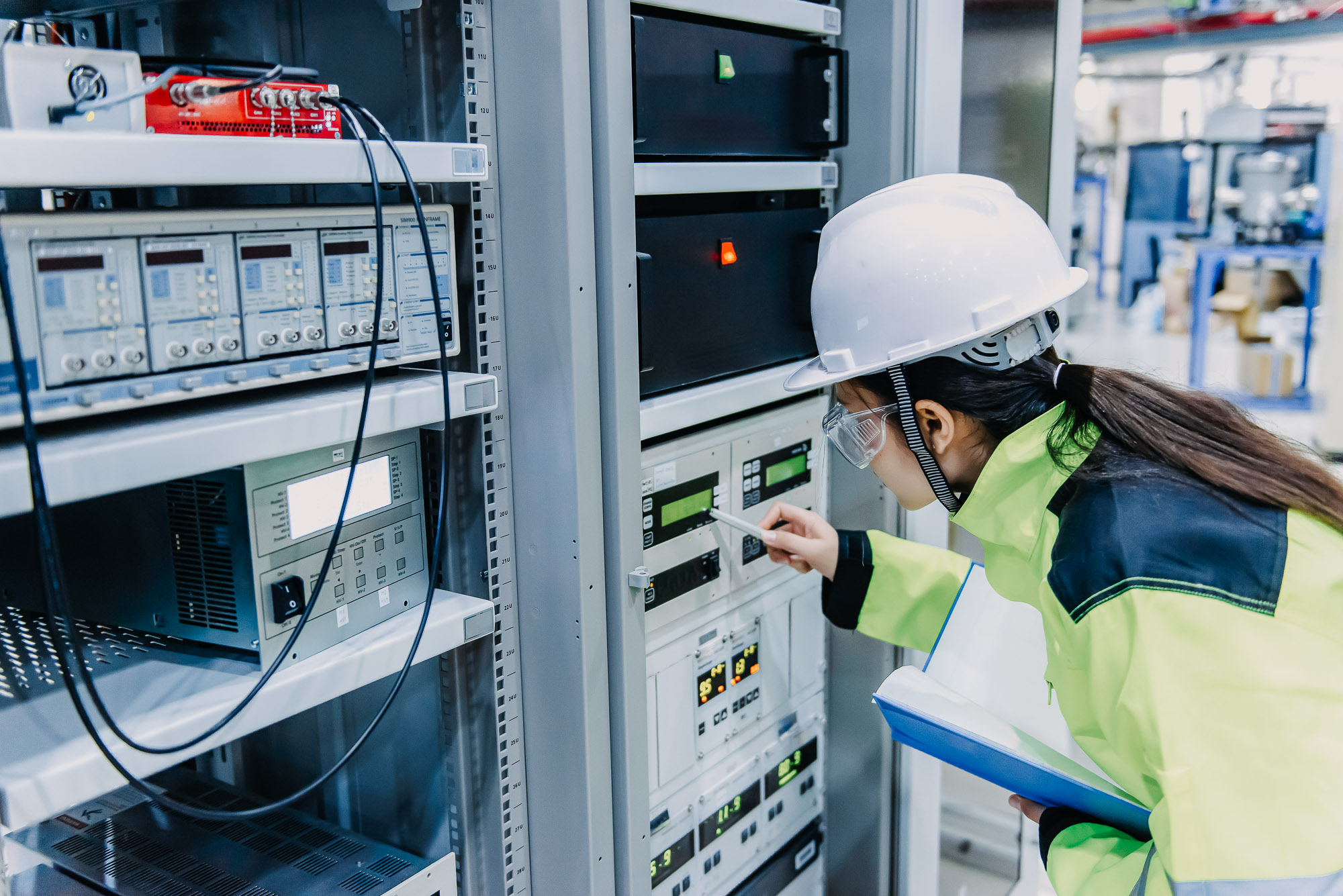
Most people think of predictive maintenance as the application of vibration, ultrasound, thermography, oil analysis, or motor current analysis to rotating machines. The site team looked at PdM as a way to get asset information on rotating and non-rotating equipment. They installed vibration sensors on pumps, motors, and fans, and a range of sensors on non-rotating assets such as steam traps, filters, and HVAC ducts. Some of the less common applications that are being monitored include:
- Measuring filter differential pressure using magnahelic gauges: This measures the air flows back to the unit and after the filter. Sensors are also monitoring the supply air temperature, which gives an indication of both the asset condition and the ability to meet the process demands.
- Monitoring steam traps using ultrasound and temperature monitoring: Steam traps remove condensate from steam. When a steam trap fails, it causes energy and monetary losses. Failed steam traps can lead to production stops, which was happening in some units.
- Monitoring current and amp draw on each leg of the motors: This allows the team to extend the intervals between infrared inspections. This is especially effective for variable frequency drives and motors that are not on active control systems.
One of the biggest challenges was getting reliable WiFi in the places where it was needed. There was WiFi throughout the facility, but some gateways were added in order to support the predictive maintenance system. C&W Services was able to use the guest network for some areas and set up a separate Petasense network system for others.
The assets being monitored were in separate mechanical rooms and on the roofs. The site was monitoring air handling units, and it is difficult to get reliable WiFi into the metal enclosures. Power was not available throughout the facilities, which limited where gateways could be installed. Cooling towers and other structures were a distance from the main building with limited power and network options.
Setting up or using an existing wireless network is often overlooked, and can be a challenging part of getting the program going. Without reliable infrastructure, the sensors can’t collect and transmit data, and analysts can’t see what is going on. Areas that are particularly difficult to get connectivity are those with lots of concrete, metal enclosures (e.g., AHU) and water. A site survey can help to determine where there are connectivity issues, and can determine which assets are able to be monitored with the available wireless network.
In order to show the effectiveness of the program, the site operations team set clear goals for maintenance and operators. The goals are visible and tracked daily, and results are presented regularly to the pharmaceutical company. Failure avoidance, energy and cost savings are captured and documented. The team now showcases a “Reliability Board” in a main hallway to drive awareness.
The change in the maintenance culture has led to a more engaged and proactive workforce. By encouraging ownership from the operators, understanding asset criticality, improving PM tasks, and setting up wireless PdM systems to predict downtime, the site has moved from reactive to predictive maintenance. Benefits have been:
- Improved equipment reliability: 31 problems were found within the first two months of PdM
- Reduced downtime: The response due to failure dropped from 29 percent to 9 percent
- Improved training: Learning the sensor operations also enforces PdM strategy
- Increased PM intervals: 2X extension of PM intervals on monitored systems
- Energy reduction: Less stream and condensate loss and more efficient equipment operation
Before the maintenance transformation, the facility experienced a bearing or belt failure on an average of every 48 days. This has now been extended to an average of once every six months. With the system, now they are able to detect loose belts, soft foot on motors, bearings and motors needing grease, and failed steam traps. The program has had a huge impact in terms of reliability.
This major pharmaceutical site has achieved zero downtime in the facilities for the first half of 2019. In the previous year, there were four downtime events, one of which was in the facilities and caused significant production downtime.
Companies in industries such as oil and gas or power generation have used PdM for 30 years, but these technologies were expensive and reserved for critical assets. With the advent of low-cost wireless sensors and increased computing power, companies across industries can monitor more assets, provide greater insights and generate more value from their program.
IIoT technology can be an enabler to improved maintenance practices, but it cannot be expected to solve all maintenance challenges. Companies looking to implement IIoT should consider the dimensions of culture, process and technology, in order to adopt a true reliability mindset.