“By implementing a sound scheduling program, performance will be calibrated for more efficient and effective service delivery.”
From Scheduling: The Key to Improving Labor Utilization, Backlog Management, and Effective Management of Maintenance Workforce Capacity, presented at IFMA 2023 by:
David Auton, CRL, FMP & SFP, MBB, cGMP
Vice President, Engineering & Maintenance
david.auton@cwservices.com
Ali Mohammed, CRL, LSS, cGMP
Senior Director, Engineering & Maintenance
ali.mohammed@cwservices.com
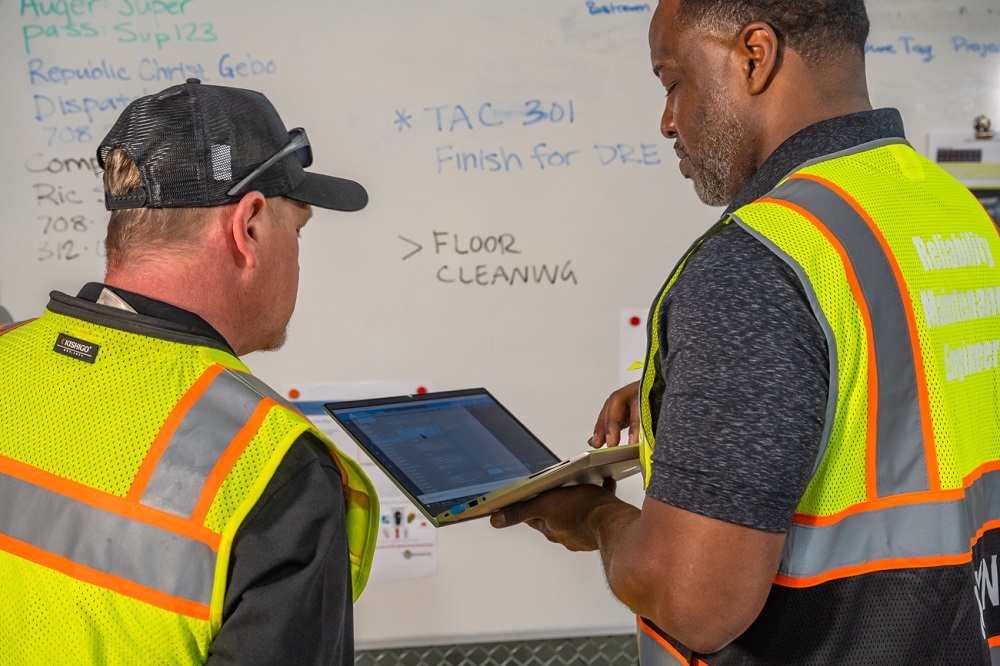
Every facility manager aims to be effective and productive, which requires efficient utilization of their maintenance team. Facility managers are expected to manage their teams to achieve key performance results. Despite desires and expectations, many organizations face challenges in workforce management and are left to justify the structure or need of their team. Facility managers often get caught between the workload that cannot be completed and costs that continue to rise. This causes one to ask many difficult questions: Is your team staffed appropriately? Do team members have the right skill set to complete the work? What are ways to maximize productivity within a team?
Scheduling can be a powerful tool to help facility managers understand effective methods for achieving an efficient workforce. Effective scheduling can also identify other workforce components to improve the productivity of your team. By implementing a sound scheduling program, other areas can be better observed, and performance will be calibrated for more efficient and effective service delivery.
What is scheduling?
Scheduling, a recurring activity at various time intervals (annual, monthly, weekly, and daily), captures alignment between identified work in the system of record, operational demands, and labor capacity, to be completed within a designated work period. Scheduling is a balancing act between operational needs and available labor capacity. The day-to-day schedule is a refinement of yearly, monthly, and weekly demands and requirements. That said, an effective schedule can only be built by understanding those demands. This should increase the awareness that some coordination and preparations are needed to achieve a solid scheduling regime. This regime will incorporate both operational demand and the longer-term strategic objectives.
What is the goal of scheduling?
The goal of scheduling is to fully utilize the labor capacity and manage any backlogged work appropriately. The benefits of scheduling are achieved when labor utilization, backlog management, and work capacity are optimized.
Labor Utilization
Many activities for Facility Managers are not considered “technical service delivery” items. Such items include meetings, training assignments, and shift meetings that cannot be directly attributed to identified work assignments. These day-to-day activities affect the ability to accurately account for the labor if they are not included in the labor utilization calculations. To understand current utilization, first determine how many hours of available technician time is captured on work orders. From there, subtract the “non-value” actions of meetings, trainings, and other non-technical activities, and calculate the overall average capacity utilization.
As a best practice, at least 85% of available hours should be applied to assigned work. If your team is struggling to accomplish this, you can read more in the 8 Golden Rules of work management to address accomplishing better labor recording.
Effective scheduling practices will enable maintenance operations to improve work management practices and maximize labor utilization.
Work Backlog Management
The work backlog includes defined tasks and work that has yet to be completed. The backlog can include both past due work and work due for completion in the future. It is often misconstrued that only past due work is in the backlog. Simply put, if we stop accepting any new work, backlog is the work in the pipeline that needs to be completed.
A healthy backlog for a fully staffed proactive maintenance organization lies between 4-6 weeks. A backlog of less than 4 weeks indicates high reactivity, ineffective work management practices, or a potentially overstaffed team. A backlog greater than 6 weeks indicates either poor culture (lack of prioritization or oversight), ineffective work management, or a potentially understaffed team.
Effective scheduling practices will enable maintenance operations to improve work management and appropriately manage work backlog.
Workforce Capacity
Workforce capacity refers to the amount of available workforce time that can be allocated to upcoming tasks. The capacity to make optimal use of the workforce’s available time differs site to site and organization to organization and relies on the maturity level of maintenance operations and organizational culture.
Certain highly reactive maintenance operations allocate a predetermined portion of full workforce availability to ensure the completion of reactive tasks. However, if this approach is initially chosen, efforts must be expended to eventually get to the ideal practice of utilizing 100% availability. Additionally, certain maintenance operations with low reactivity may choose to load more work than the available capacity, assuming inefficiency in the work plans and establishing stretch goals. In the short term, this approach may be feasible to remove inefficiencies from operations, however, in the long term this will result in a burnout of employees.
The optimal approach is to allocate tasks and fully utilize every time unit within each work period for all available resources, with the objective of attaining the highest standard of practice. Teams should remain effectively occupied with tasks and appropriate breaks without frustration and without pressure to rush.
Effective scheduling practices will enable maintenance operations to balance work content with appropriate workforce capacity and implement sustainable operations.
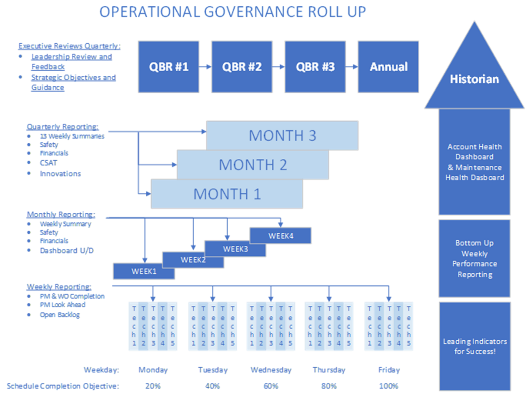
Scheduling Challenges
Scheduling can provide significant benefits for a facility team to be more efficient with their time which will lead to greater service capability. There are also several barriers for effective scheduling that can be challenging for teams. Expectations, training, alignment, roles, behaviors, and cultures can all be identified and resolved with the proper procedures in place. Expectations
A lack of clear communication and expectation by leadership to enforce standard operating procedures can result in missed execution. Leadership must communicate and set clear guidelines that teams are expected to schedule their work and that they will be monitored. Standard operating procedures must be defined and enforced.
Training
The team must have adequate training and guidance on proper scheduling. This may include taking classes, working toward certifications, or providing mentorship. Until scheduling is routinely executed well, teams may not grasp the basic concepts and execute consistently. Training is a pivotal part of adoption.
Alignment
The organization must demonstrate how effective scheduling contributes to both team and individual success. The value must be understood by individual contributors to achieve alignment and adoption.
Clear Roles
A lack of clear roles and responsibilities will result in continual confusion about where responsibilities lie for each team member. This will inhibit adoption and success. Process maps should include clear roles (not just titles) defined and assigned to individual team members to ensure each person knows their contribution to the successful scheduling process.
Reactive Behaviors
Highly reactive organizations find scheduling difficult. The phrase, “no time to do right but always time to do over!” comes to mind. A lack of scheduling adequate time and correct repairs often contribute to this self-reenforcing condition. Fix it the first time, fix it correctly, and fix it permanently to escape this cycle.
Organizational Culture
Organizational culture must build trust and communicate transparently. If the organization only communicates “what” to do without a “why,” members may feel disconnected and lack an understanding of the program value. The culture should exhibit a desire for quality (pride in one’s work) and a commitment to be transparent. All members should be able to identify their contribution to the quality goal.
Scheduling Tools
Having a process is much better than having a goal. A commitment to improving the scheduling process enables improvements with each subsequent schedule. Having a simple goal of “scheduling all my work” allows for missing the goal with any unscheduled assignment. Having a process of improving scheduling each week enables the ability to evaluate what works well and what parts of the process need improvement. The first activity should be to map out the process to accomplish a desired state for a typical day and a typical week. Daily shift activity may be the easiest to map, because it will highlight what is expected each day and enable identification of where unexpected events arise. Understanding what is needed to follow the daily processes should be the objective.
Typically, scheduling will follow a weekly process. Some organizations use monthly scheduling; some use daily scheduling. Depending on the organizational needs, the ideal takt time should be determined. Although scheduling should follow the takt time of the organization, the scope and fundamentals should be constructed from the strategic objectives. Routine scheduling enables the long-term strategic goals of annual Preventive Maintenance delivery, reliable systems, and a balanced workforce.
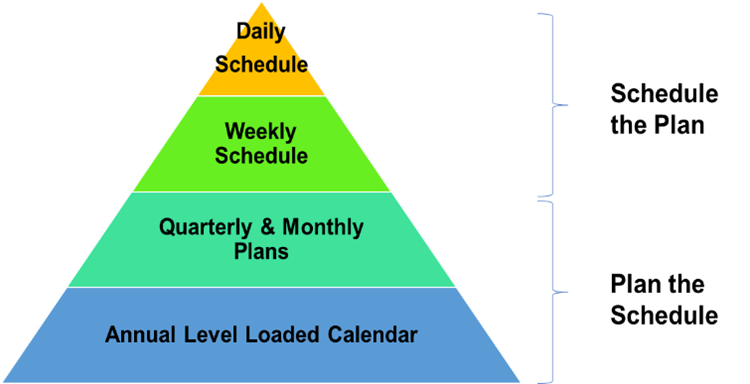
Key Scheduling Components
The primary components of an effective, strategically aligned schedule include:
Long-Term / Annual Calendar Plans
Core to the strategic plan, this is the What, When and Where. This addresses the level loaded Annual Preventive Maintenance Program and Shutdown Event Schedules.
Short Term / Quarterly & Monthly Plans
Refining the strategic plan of What, When and Where. This includes Preventive Maintenance, Projects & Events, Long Lead Time Corrective Maintenance.
Weekly Schedule
Refining the What, When, Where and adding Who based on resource and skill capacity, the plan is becoming more solidified.
This includes Preventive Maintenance tasks, projects, and events, as well as all corrective maintenance and requested work completed according to operational requirements and assigned to the designated individual(s) within a specified timeframe.
Executable (Daily) Schedule
This is the leading event that needs to be executed by the individual employee within the daily work assignments. The execution of the daily assignments is a leading indicator in determining if our strategic and operational objectives are achievable.
Best Practices
To achieve success, it is best to start with a plan and ensure the team members are on board. The best way to get the team aligned for success is to focus on expectations, processes, tools, and effective communication. It is best practice to communicate the benefits and create an expectation of progressively improving with each cycle. This should include the quantifiable measures used (on-time delivery, backlog management, etc.). Teams should also:
- Establish and document the standard work management process that includes clarity of roles and responsibilities.
- Train all roles on the standard work management and scheduling process.
- Establish the tools that will be used to manage the scheduling and how they are to be used and configured.
- Define what scheduled means regarding work status. Establish a visual dashboard of work scheduling that communicates scheduled work and progress to completion.
Now that there is a plan to achieve scheduling, ensure the work data is managed effectively. This includes ensuring Preventive Maintenance (PM) plans are established for all maintenance needs. There should be a level loaded annual PM calendar, with automatic PM generation, 4-6 weeks prior to desired completion. All work identified must have a valid work order, and no work is to be executed without a work order. All work orders must have sufficient information such as type, priority, target completion date, etc. Critical information not provided by the requestor must be obtained. All work must go through planning and work orders must include planning for skill and time estimates.
Conclusion
The ability to utilize the maintenance workforce most efficiently requires a solid scheduling program. Facility managers both desire and are expected to utilize the maintenance workforce effectively. Good scheduling is the pathway to operational performance and financial controls of the maintenance program. Challenges to effective workforce management and justification of resources are often associated with work getting completed in a timely fashion. Maximum team productivity and satisfaction is achieved through understanding and adherence to a solid scheduling program. By implementing a scheduling program, performance can be calibrated for more efficient and effective service delivery.