Our client is a leading specialty semiconductor company that provides design, development and fabrication services. We provide janitorial and controlled environments cleaning for multiple semiconductor plants with 3.6 million square feet of offices and 1.1 million square feet of fabrication space. More than 5000 customer employees work at these sites, which are in operation 24/7.
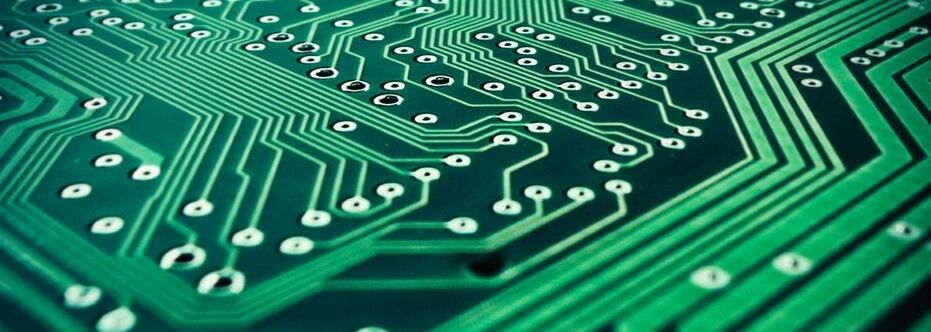
OUR APPROACH
Our client is a leading specialty semiconductor company that provides design, development and fabrication services. We provide janitorial and controlled environments cleaning for multiple semiconductor plants with 3.6 million square feet of offices and 1.1 million square feet of fabrication space. More than 5000 customer employees work at these sites, which are in operation 24/7.
THE RESULTS
- In reviewing the cleaning Scope of Work and protocol for manufacturing space, we identified adjustments that reduced the amount of air contamination measured by EM/Particle counts. Adjusting the times and methods for vacuuming and closing certain process aisles lowered the particle counts without cost increase. The result was an increase in yield production.
- Our team identified that the site’s existing production waste collection points were inefficiently placed, causing frequent overflows at consistent times of the week. We developed a way to change pickup to more effective extraction points, increasing efficiency and decreasing overflow problems without additional cost or change to our Scope of Work.
- C&W Services cleans the site’s restrooms regularly – so often that we may notice a problem before anyone else. Our team noticed an overflow of waste water, and quickly brought in vendors to diagnose the problem. The investigation found a deliberate sabotage of the waste line, which caused a major backup. Over three days, we worked with our vendors to fix the issue, clean the space, and monitor the situation to identify the culprit. This attention to detail not only corrected the situation but avoided the potential for a larger overflow that could have affected fabrication production.
- During a power outage in the below-grade sub fabrication space, low light hindered an employee evacuation. While the space was not part of our current scope, we partnered with the space’s director to thoroughly clean the floors and then painted a path of fluorescent arrows to guide future evacuations. As a result, we were awarded cleaning of the space on a permanent basis.
ACCOUNT OVERVIEW