Our client, a major Global Biopharma Manufacturer, is one of the world’s leading pharmaceutical companies. Founded in 1885 and headquartered in Germany, the company researches, develops, manufactures and markets new medications of high therapeutic value for human and veterinary medicine. C&W Services oversees the facilities maintenance in California, Missouri, Connecticut and Ohio for the Global Biopharma Manufacturer.
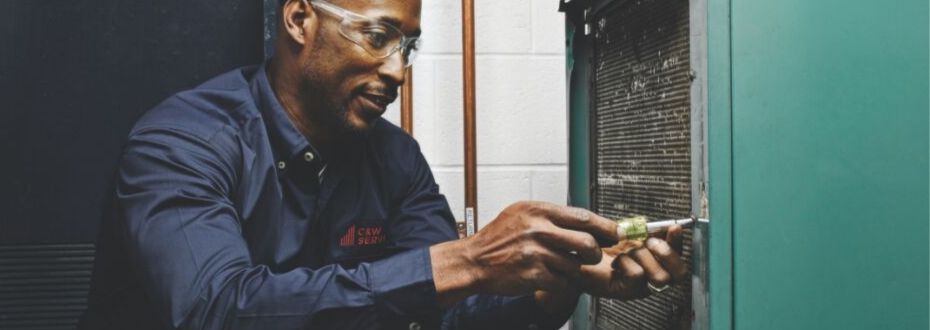
CHALLENGE
Our client needed to perform a shutdown to boost manufacturing capabilities by upgrading utilities, replacing some older pieces of equipment and increasing capacity. However, they couldn’t shut down the entire facility. Critical systems needed to remain operational during the planned shut-down.
SOLUTION
C&W Services helped the client develop a methodical approach that minimized production run impacts and negative effects on company profitability. We brought in a team of experts to oversee the technical planning of the project, which included de-energizing equipment for service; Lockout-Tagout (LOTO) of systems for connectivity; safe shut down and start up; and the effective managing of utility supply through the expanding campus.
THE RESULTS
- Over an eight-week period, the shutdown accomplished the following, on budget and with zero safety incidents:
- Three hundred electrical LOTOs and 100 mechanical LOTOs
- Seventy-five Corrective Maintenance Work Orders and 187 Preventative Maintenance Work Orders.
- Effective resolution of all unplanned failures and repairs
- Kept the site operational during a month-long loss of power by maintaining generator support. This was to add a redundant grid supply and automatic power switching (ATS) upgrades.
- Assisted with the BMS virtualization, which included unplanned system failures response.
- Provided escort service for external technical support teams during the shutdown which greatly helped the continuity of the project. In addition, it saved the client from significant security costs.
- Aligned the annual boiler PM to coincide with the shutdown which avoided the cost of a rental boiler and saved client over $100,000.
- Scheduled and completed a PM on the Deaerator tank during the shutdown which had not been done in the past.
MEET OUR TEAM
Learn more about how we helped this client with a new procurement method that allows for quick turnaround times and helps secure the correct pricing, quality, and delivery. We also oversaw a reorganization of the MRO warehouse to a GMP compliant standard, and maintain proper spare part inventory levels in the MRO warehouse to ensure that there are no delays or interruptions to production.
ACCOUNT OVERVIEW